Industrial water softeners and filters
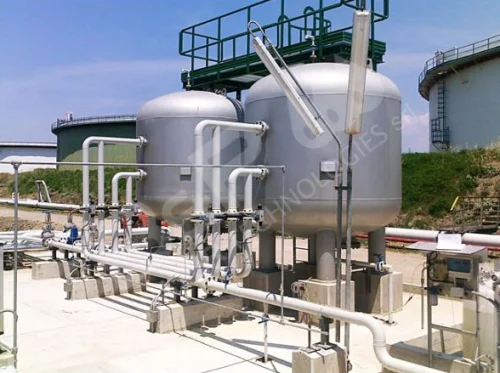
WATER SOFTENING: AN OVERVIEW
B&P Water Technologies has a deep experience in supplying customized solutions for the industrial and civil water softening, filtration, iron removal and sterilization, for water flow rates in a range of 1-300 m3/h.
Softening can be achieved by means of water softeners filled with resins (FDA approved). Softeners can be supplied both in single and duplex configuration, with timer/volume based regeneration sequence.
Filtration can be achieved by means of sand and carbon filters, iron removal filters, self-cleaning filters, cartridge filters.
Sterilization can be achieved by means of UV sterilizers and chlorine dioxide injection.
Water Filtration – Sand filters, Activated carbon filters, Cartridge filters
Primary water are received from well, rivers, lakes and, prior to any use, must be free from any kind of suspended solids. For these particles removal of B&P Water Technologies can offer various systems of filtration with self cleaning filters, sand filters and with cartridges.By means of cartridge filters the filtration limit is equal to 2 microns.
The use of activated carbon filter allows to obtain water free from chemical components like free chlorine, phenols, etc.
This kind of filtration can be used also to deodorize water.
The filters can be supplied in single or battery configuration with manual or automatic backwash.
Industrial softeners
Water represents the raw material in the most part of the industrial processes. The raw water is usually fed from the public network or from water wells. The raw water contains some ions, like calcium and magnesium, that determine the hardness and are responsible of scaling in the hydraulic circuits. At temperatures higher than 40°C, calcium and magnesium deposits can build up in pipes, reducing flow to taps and appliances. In water heaters, these minerals generate a scale build-up that reduces the efficiency and life of the heaters and boilers. Another effect of hard water is that soaps and detergents lose some effectiveness. Instead of dissolving completely, soap combines with the minerals to form a coagulated soap curd. Because less soap is dissolved, more is required. The soap curd can keep dirt trapped in the fibers, and it can stiffen and roughen the fabric. It is evident that a raw water conditioning will give strong advantages in the process managements of the industrial laundries. Water conditioning can be done by ion exchange softeners.How water softening works?
A standard water softener works by allowing hard water to filter downwards through a bed of ion exchange resin. The ion exchange resin attracts the calcium and magnesium ions (hardness) and replaces them with sodium ions, which are less problematic for water systems and will not cause scale build-up. Once the ion exchange resins are saturated with hardness, the regeneration sequence on the water softener begins.The water softener's regeneration sequence begins with the backwash cycle. The backwash cycle reverses the flow of the water to pass upwards through the ion exchange resin bed. This operation frees the beads of the ion exchange resin ready for the next step in the regeneration sequence.
In a water softener's regeneration sequence is to saturate the ion exchange resin with a brine solution. It is during this step that the ion exchange resin releases the calcium and magnesium ions and replaces them with sodium ions.
Both the calcium and magnesium ions flow along with the water and excess brine solution to drain.
The frequency of a water softener's regeneration cycle is usually preset, using a timer or a counter-signal from a water meter.
Ion exchange softening is a well-known technology widely used for civil and industrial purposes.
Advantages
The advantages of the ion exchange softening can be summarized as follows:- Technology consolidated and well known
- Low equipment and installation costs
Cartridge filters
Cartridge filters are:
- sediments filters, installed to reduce the amount of sediments transported by the fluid trough filtration;
- are preferable for systems with contaminations lower than 80-100 ppm;
- cartridge filters can be used a "second stage" filtration downstream the sand filtration (for example in the pre-treatment of reverse osmosis plants), where a more accurate filtration is required;
- cartridge filter can be surface or depth-type filter: depth-type filters capture particles and contaminant through the total thickness of the medium, while in surface filters (that are usually made of thin materials like papers, woven wire, cloths) particles are blocked on the surface of the filter.
Surface filters are best if filtering sediment of similar-sized particles shall be achieved. If all particles are, for example, five micron, a pleated 5-micron filter works best because it has more surface area than other filters. Compared with pleated surface filters, depth filters have a limited surface area, but they have the advantage of depth.
It can be generally stated that if the size of filter surface is increased, higher flows are possible, the filter last longer, and the dirt holding capacity increases. Cartridge filters are normally designed disposable: this means that they have to be replaced when the filter is clogged.
UV Sterilization
The simplest way to disinfect water is to expose it to ULTRAVIOLET LIGHT. THE LIGHT OF THE SUN. ULTRAVIOLET is invisible radiation within a range of the solar spectrum. Such radiations may be divided into two different bands: A) LONG WAVE: or infrared energy such as heat. B) SHORT WAVE: such as invisible ultraviolet. Appropriated Ultraviolet wavelength is GERMICIDAL, it destroys BACTERIA, MOLDS,YEASTS AND VIRUSES INSTANTLY. Disinfection of water using ultraviolet light (UV) is a proven technology. This safe and effective physical disinfectant is suitable for both large and small applications.
Ultraviolet light, better known as UV, is one energy region of the electromagnetic spectrum. In this spectrum UV lies between visible light and X-rays.
Microorganisms include several distinct groups of disease causing germs, differing widely in form and life cycle, but resembling one another in their small size and relatively simple structure. Microorganisms encompass five major groups: Viruses, Bacteria, Fungi, Algae and Protozoa. A basic bacterial cell has the following main structures: the cell wall, cytoplasmic membrane and nucleicacid. The target of UV disinfection is the genetic material, nucleic acid. Microbes are destroyed by UV if the light penetrates through the cell and is absorbed by the nucle The absorption of UV light by nucleic acids causes a rearrangement of the genetic information which interferes with the cell's ability to reproduce. A cell that cannot reproduce is considered dead since it is unable to multiply to infectious numbers within a host. The maximum absorption of UV light by the nucleic acid. DNA, occurs at a wavelength of 260 nm. The germicidal lamp emitting UV at 254 nm is operating very close to the optimum wavelength for maximum absorption by nucleic acids, Microorganisms differ in their sensitivity to UV light. This variation may be due to cell wall structure, thickness, and composition; to the presence of UV absorbing proteins or to differences in the structure of the nucleic acids themselves. Waterborne diseases may be caused by a wide variety of pathogenic microorganisms.
Disinfection of drinking water with UV must ensure a maximum dose to cover this wide variation of UV sensitivities (eg.) 99.9% reduction of E. coli requires a dose of 7,000 microwatts cmq, whereas a similar reduction of protozoa cysts requires a dose of approximately 105,000 microwatts cmq. UV Dose is a product of intensity multiplied by contact time. Intensity is the amount of UV energy per unit area measured in microwatts per square centimeter. The contact time is the amount of time the solution is exposed to UV in the reactor (measured in seconds). Therefore UV Dose is expressed in microwatt seconds per square centimeter. Survival curves demonstrate the susceptibility of a specific organism to different doses of UV. Effective UV dosage is reduced by a loss of UV in passing through water.
Transmittance is a measure of the amount of UV energy, that will pass through 1 centimeter of water. This is measured using a UV spectrophotometer. The National Sanitation Foundation (NSF) UV Disinfection Committee has suggested that drinking water should have a UV transmittance greater than 75% at a wavelength of 254 nm. Appropriate water treatment devices can be used to reach the required level of transmittance. Water quality influences the effectiveness of all types of disinfections. including UV. The three major concerns affecting UV performance are suspended solids, absorption of UV and coating of quartz sleeves. All reduce the intensity of UV energy reaching the microbes, Suspended solids create shadows that prevent UV energy from reaching microbes. This can be overcome by designing the reactor to create turbulent flow patterns bringing microbes out of shadowed positions, but microbes within particles cannot be reached without adequate intensity to penetrate the particles. Absorption of UV light by various soluble molecules reduces the amount of UV enegy available to penetrate through the water layer to reach the nucleic acids, Humic acids, tannins and iron, commonly found in drinking water are examples of UV absorbing compounds.
Calcium and magnesium (hardness), manganese and iron at levels that meet current potable water standards will not affect the UV disinfection process, but over a period of time these elements may precipitate on the lamp sleeve and reduce the intensity, which enters the water layer. These conditions can and should be pretreated using proven technologies. UV manufacturers produce systems ranging in size from 0.5 GPM to several hundred GPM. The key elements of all UV systems are the ballast and lamp combination, a teflon or quartz sleeve to protect the lamp, and a properly designed reactor chamber. For maximum efficiency, the UV lamp must be driven properly to ensure optimal germicidal output. The ballast is the controlling device that drives the lamp at the desired electrical conditions. The germicidal output of UV lamps gradually decreases over a period of use and most manufacturers claim that their systems have an effective life ranging between 6,000 and 12,000 hours. For optimal UV output the lamp operates at 40' C. The sleeve separates the lamp from the water, to provide electrical safety and to maintain lamp operating temperature so that the UV output does not fluctuate with water temperature. The hydraulics of the reactor determine the contact time. Therefore UV output is affected by flow rates, flow patterns in the reactor (short circuiting), shadowing in the reactor, and lamp configuration in multiple lamp systems. When designing UV systems the theoretical calculated contact time, and the actual contact time can vary greatly. This variation will influence the actual UV dose compared with the calculated dose (Dose = Intensity x Time) by decreasing the value of time. The actual UV dose may be determined with a bioassay. The most common UV applications fall into the following categories. POU, POE and industrial. When installing a POU system, it is usually installed on the cold water line and the disinfected water should be dispensed from a separate faucet to ensure that the water does not become re-contaminated by using the same faucet that is used for untreated water. POE equipment for home applications is installed prior to the line split for hot and cold water. Most large industrial applications are usually site specific, depending on their application, what microbes they are concerned with, the water quality, and effluent discharge regulations. In most UV applications, following a few simple rules will eliminate most UV problems. When you install a UV system ensure that you leave enough clearance so that lamp replacement and any maintenance the system requires can be done without having to remove the system. The simplest way to size a unit is to determine the capacity that the distribution system will provide and install system that will disinfect that volume (gallons/minutes). By following this procedure, there will be minimum effect on any pressure loss.
If flow capacity varies greatly, it is best to install a flow controlling device to restrict the volume to the designed capacity of the disinfection system. If the volume to be disinfected exceeds the capacity of the UV system, the loss of contact time will reduce UV dose. Since UV is a physical process, (nothing is added to the water) it does not leave a residual disinfectant in the distribution system. The distribution system should be disinfected (shocked) when a UV unit is installed. All other pretreatment devices should be installed ahead of the UV system. There may be a few applications where this doesn't apply (such as sub-micron filtration at point of use) The distribution system should be checked for places where microbial contamination could collect. These dead spots should be eliminated from the distribution system. Shocking with a bleach should kill any microbes remaining in the plumbing system. UV disinfection standards are still based on the 1966 statement by the U.S. Department of Health, Education and Welfare. That UV disinfection equipment required a UV dose of 16,000 nw. sec. cmq.
Contact the water desalination company
For any enquiry/info and estimate of costs, please fill the form below
and you will be contacted by our specialist as soon as possible.